MAXIMIZING HPHT DRILLING EFFICIENCY & WELL PRODUCTIVITY THROUGH OPTIMAL HPHT WELL DESIGN
By Dr Michael Gibson
This first section of the updated Wellideas HPHT (High Pressure High Temperature) Sections shows how Wellideas.co.uk has improved its HPHT services, particularly now that oil and gas prices have recovered very significantly from the Global CoVid pandemic. Wellideas.co.uk is servicing a considerable number of Operators and Drilling Contractors in HPHT, particularly since the oil and gas prices on the worldwide market have increased so much (literally, a 40% increase).
This first section gives great insight to HPHT Oil & Gas Operators, HPHT Drilling Contractors and Service Personnel as to why certain areas must be covered, when they should be covered, and how they should be made.
Wellideas.co.uk are pleased to announce this update to their HPHT High Pressure High Temperature Well Design Services in this new era of high oil and gas prices. New drilling technology and deeper understanding of HPHT reservoirs and geology, coupled with MPD Managed Pressure Drilling Services and a plethora of HPHT tools and equipment are now able to unlock oil, gas and condensate from a variety of HPHT reservoirs on land and offshore. This update follows HPHT Well Design Services provided by www.wellideas.co.uk to several Operators following the recent quite dramatic rise in oil and gas prices – particularly since HPHT reservoirs can be very prolific in terms of their production rates – providing the well is optimally designed.
The HPHT Well Designs included: 1) Reservoir & Geological Analysis; 2) Risk Assessments; 3) Drilling Program Writing; 4) Well Test Program Writing and 5) Completion Program Writing – all with the objective of maximising efficiency, cost reduction and hydrocarbon production.
Today’s high drilling costs – particularly with respect to HPHT wells – necessitate the avoidance of problems, rig down-time, maximum drilling efficiency and maximum hydrocarbon production. Many “New Operators” and “New Drilling Contractors” have never drilled into HPHT reservoirs before, and so are reliant upon expert HPHT Consultancy experts to maximise the return on their investment – and to ensure that the well is drilled safely, optimally and without monetary loss, human life loss and environmental damage. Otherwise, HPHT wells can be lost or cost far more than budgeted for. Thus, HPHT wells require excellent Drilling Engineering / Well Planning, Drilling Consultancy and Drilling Operations – both onshore during the Client’s planning phase and offshore in the operational phase. And key to this last point is an excellent rig with a fully HPHT trained drill crew.
The key areas which Wellideas.co.uk focus upon are those areas which often, typically, the Operator and Drilling Contractor “overlook”. These areas are typically as follows: –
- Pore Pressure – Are there any variations or pressure “ramps”?
- Fracture Pressure – Are there any variations or “ramps”?
- What is the “Optimal Mud Weight Window” including ECD (Equivalent Circulating Density)?
- What LCM (Lost Circulation Material) is required?
- What is the Cementation Design and it’s ECD (Equivalent Circulating Density)?
- If there’s a “Pressure Ramp” prior to entering the reservoir, will the Operator try to set the 9 5/8” / 9 7/8” casing “deeper” or set a Drilling Liner?
- Hydrogen Sulphide Issues
- Carbon Dioxide (plus water) Issues
- Hydrates / Waxes / Asphaltenes
- Reservoir Collapse Pressure over time.
IADC & SPE Technical & Operational Papers about HPHT Well Failures typically point to the following reasons as to why HPHT Wells “Fail” – And why cost-over-runs can be several $Million – and why well productivity can be lower than estimated. In summary, the reasons cited are as follows: –
- Poor Operator, Drilling Contractor & Service Company Philosophies
- Inadequate well design
- Poor / Inadequate Management Systems
- Poor / Inadequate Well Design Standards
- Poor / Inadequate Operating Philosophies, Procedures & Practices
- Not Understanding the Reservoir and / or Over-lying Geology
- Poor Intra-Departmental and Intra-Company Communication
- Poor Operator / Drilling Contractor & Service Company Interface Documentation
- Poor / Inadequate Contingencies
- Lack of Operator / Drilling Contractor / Service Company Expertise
- Inadequate HPHT Training
- Inadequate / Poorly Executed “DWOP” / “Teamwork” Exercises
- Poor Wellsite Supervision
- Inability of Operator and Drilling Contractor to solve and execute complex well control issues, such as “Cross-flow” and “Underground Blowout” Issues
- Unexpectedly High Pressures / Low Fracture Gradients / High Hydrogen Sulphide / Carbon Dioxide etc.
- Lack of “Contingencies”.
The first schematic, below, shows the importance of utilising “High Energy Seismic” at the earliest of “Data Acquisition” phases. For it’s vital to fully understand the pore pressure profile as early as possible. Here we can see how quickly the pore pressure rises from 15 ppg MWE to 20 + ppg MWE – which massively impacts the drilling fluid design, the casing design, the cementation design, and the choice of drilling rig.
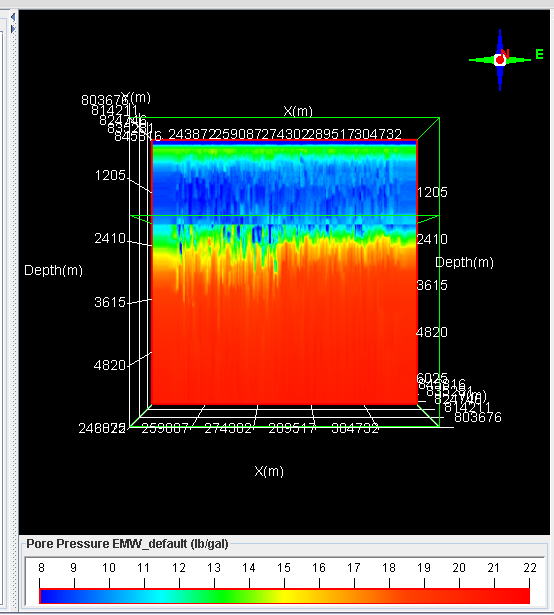
The second, schematic, below, shows the importance of highly detailed seismic evaluation of the geology over-lying the reservoir to “see” if there are any “untoward” anomalies en-route to the reservoir – such as, as shown, “Gas Clouds”. These are often typical in HPHT regions, as high-pressure gas can often “breakthrough” the over-lying reservoir cap-rock and cause high pressures (which sometimes result in “Shallow Gas Blowouts”) en-route to the reservoir.
It’s essential that all pressure en-route to the reservoir are known (or at least estimated) in order to avoid shallow gas blowouts, high pressure well control incidents and problematic downhole conditions which can cause the Operator significant cost and possible problems due to “Cross-Flow” and “Underground Blowout” situations.
Generally, the more information acquired before drilling – the better.
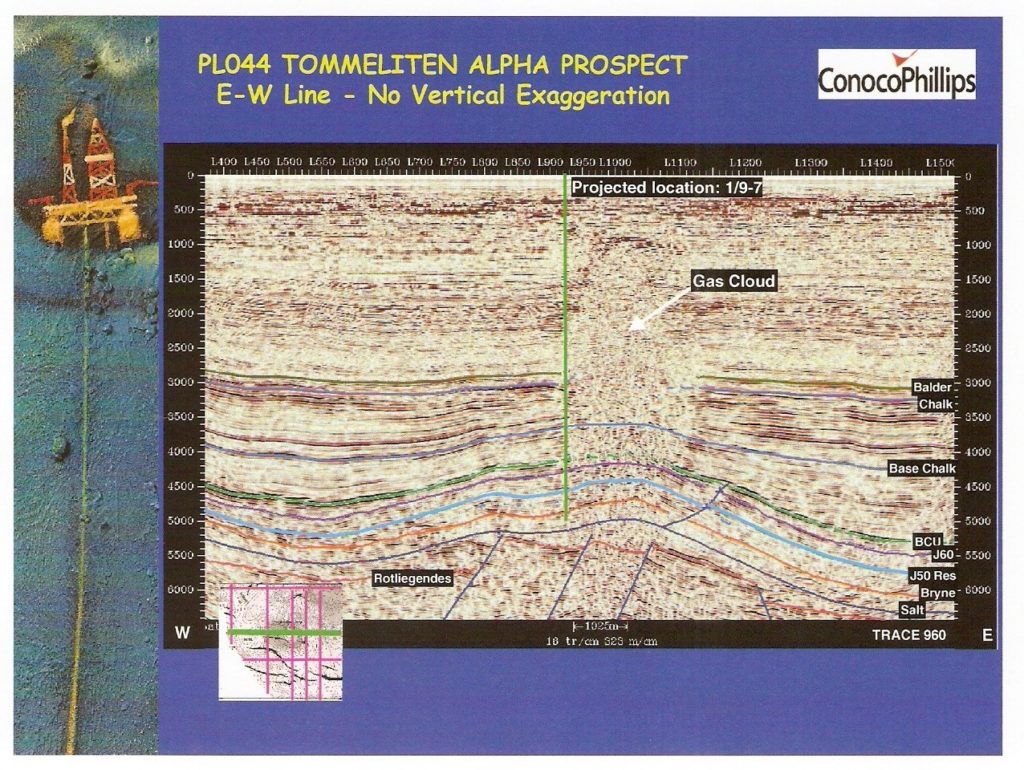
The third schematic, below, shows the temperature and pressure ranges which define HPHT, which are vital to know for drilling fluids design, cement design, casing design and rig selection etc.
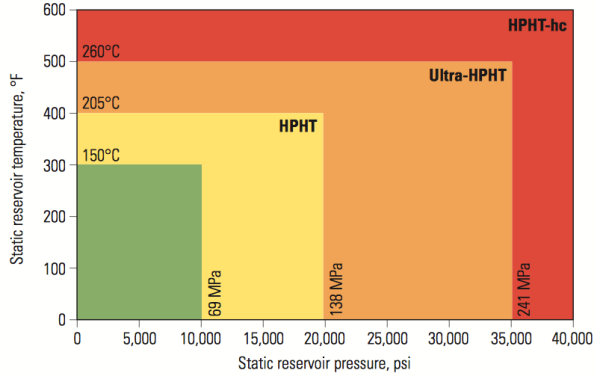
In summary, it is vital to know as much information as possible downhole before the well is drilled in order for Drilling to be a success – and, just as importantly, the Completion and Well Productivity.
Who is Dr Michael T. Gibson?
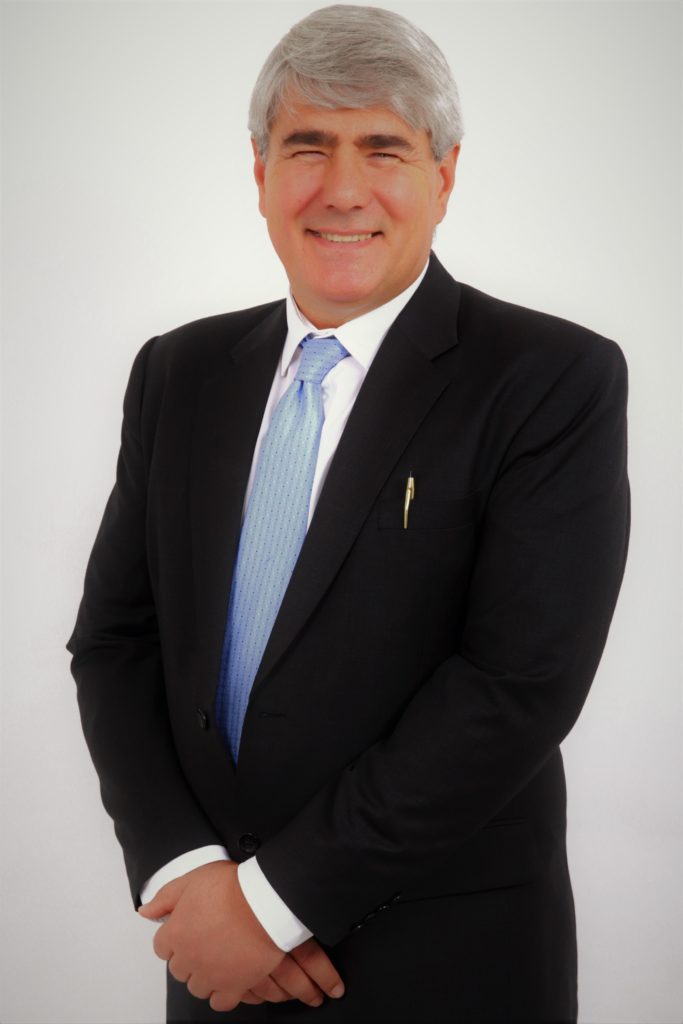


Dr Michael T. Gibson has 40 years in the Oilfield, working initially as a Drilling Engineer when he studied Mechanical and Offshore Engineering at Bachelor’s, Diploma and Master’s, Degree Level at Robert Gordon’s in Aberdeen under the expert tutelage of Professor Blythe McNaughton. He then went on to take a PHD over an 8-year period whilst working offshore as a Drilling Supervisor.
He began teaching / lecturing full-time 15 years ago in many parts of the world for Oil Companies, Drilling Contractors and Universities and has written the vast bulk of Wellideas’ material, ranging from Manuals, Pocket Handbooks, PowerPoints and Videos for the Classroom and Zoom Meetings, through to E-Learning Modules for distance learning.